Need Any
Consultation?
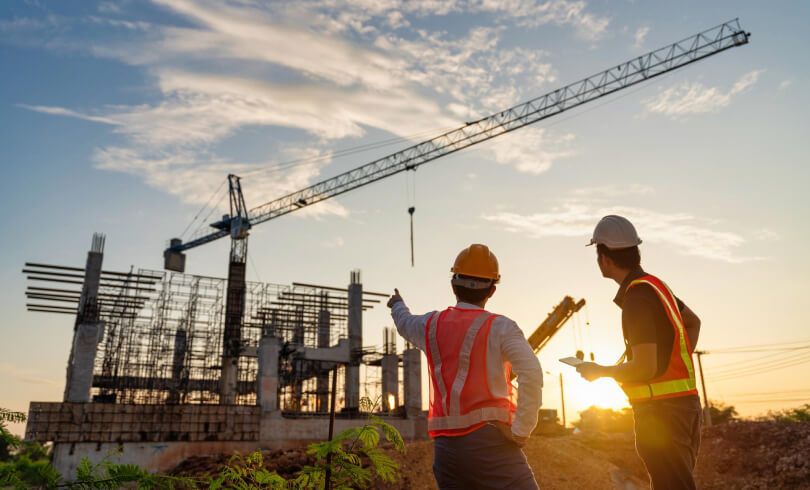
Cable Trays
Cable trays are essential components in electrical systems, designed to provide robust support and organization for cables in various settings. Manufactured from high-quality materials and treated with protective coatings, they offer durability and resistance to environmental factors. Ideal for industrial, commercial, and infrastructure applications, cable trays ensure efficient cable management, enhance safety, and simplify maintenance. Their versatility and reliability make them a key element in modern electrical installations.

Modern Manufacturing & Engineering Solutions Provider
Delivering top-tier manufacturing services with precision and innovation.
- Professional Manufacturing Services
- Dedicated Team Members
- Trusted Manufacturing Partner
Production and Manufacturing Process
Cable trays are essential components in modern electrical infrastructure, designed to support and organize cables effectively. The production of cable trays involves a series of meticulous steps to ensure durability, strength, and reliability.
- Material Selection
- High-quality raw materials such as galvanized steel, aluminum, or stainless steel are carefully chosen for their strength and corrosion resistance. The choice of material depends on the specific application and environment where the cable trays will be used.
- Design and Engineering
- The design phase involves creating precise layouts that meet industry standards and customer specifications. Computer-Aided Design (CAD) software is utilized to produce detailed models, ensuring that the trays can support the required load and accommodate various cable types.
- Cutting and Forming
- The selected materials are cut to specific dimensions using advanced machinery. The forming process shapes the metal into the desired tray configuration, whether it be ladder, perforated, or solid-bottom trays. High-precision bending and punching machines ensure uniformity and accuracy in every piece.
- Welding and Assembly
- For trays requiring additional structural integrity, welding is performed by skilled technicians. The assembly process then involves combining different components, such as rungs and side rails, to create the final product. Each piece is inspected for quality and alignment.
- Surface Treatment
- To enhance durability and resistance to environmental factors, cable trays undergo surface treatments such as galvanization, powder coating, or anodizing. These treatments protect against corrosion and extend the lifespan of the trays, making them suitable for a wide range of environments, including outdoor and industrial settings.
- Quality Control
- Throughout the manufacturing process, rigorous quality control checks are conducted. These include load testing, dimensional checks, and surface inspections to ensure that each tray meets strict industry standards.
- Packaging and Distribution
- Once the trays pass all quality checks, they are carefully packaged to prevent damage during transportation. The trays are then distributed to various sectors, including commercial, industrial, and residential projects.
Benefits of Cable Trays
Cable trays offer an organized way to manage large quantities of cables, reducing clutter and making maintenance easier. They allow for easy access to cables for inspection, repairs, or upgrades.
Manufactured from high-quality materials and treated with protective coatings, cable trays are built to last. They resist corrosion, wear, and environmental damage, ensuring a long service life even in harsh conditions.
Cable trays are available in various sizes and configurations, making them adaptable to different project requirements. They can be easily expanded or modified as the needs of the installation grow.
By keeping cables organized and off the ground, cable trays reduce the risk of accidents such as tripping hazards or electrical fires. They also protect cables from physical damage, which could lead to costly downtime or dangerous situations.
Cable trays are a cost-effective solution for managing electrical cables. Their durability and ease of installation can lead to significant savings in both initial costs and long-term maintenance.
Suitable for a wide range of applications, cable trays can be used in commercial buildings, industrial plants, data centers, and more. They accommodate different types of cables, including power, data, and communication cables.
Usage of Cable Trays
- Industrial Settings
- In manufacturing plants, cable trays are used to manage power and control cables that connect machinery and equipment. Their robust design makes them ideal for withstanding the demands of heavy industrial environments.
- Commercial Buildings
- In office buildings and shopping centers, cable trays are used to route data, power, and communication cables. They help maintain a neat and organized infrastructure, essential for the operation of modern technology.
- Data Centers
- Cable trays play a crucial role in data centers by organizing the vast number of data and power cables. They ensure that the cables are properly supported and allow for efficient cooling and airflow, which is vital for the performance of servers and other equipment.
- Infrastructure Projects
- In infrastructure projects like bridges and tunnels, cable trays provide a secure method for running electrical cables over long distances. Their design protects the cables from environmental factors and mechanical stress.
- Renewable Energy Installations
- In solar and wind energy projects, cable trays are used to manage the wiring that connects panels and turbines to inverters and the grid. Their corrosion-resistant properties make them suitable for outdoor installations.